Blog
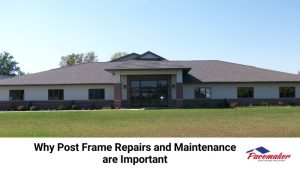
Why Post Frame Repairs and Maintenance are Important
In this post, we discuss common post frame building repairs and maintenance issues. Learn 10 areas that are most prone to deterioration over time.
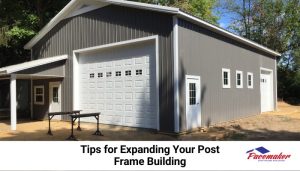
Tips for Expanding Your Post Frame Building
Expanding Your Post Frame Building is easier than other types of construction. Here are essential factors to examine before proceeding.

The Best Heating and Cooling Options for Post Frame Buildings
Heating and cooling options are essential choices when planning a post frame building. Use these tips to finding the best solution.
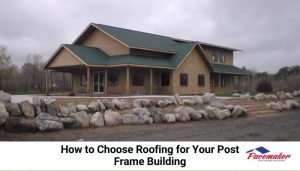
How to Choose Roofing for Your Post Frame Building
In this post, we discuss roofing for Your post frame building. We cover roof types, design and function.
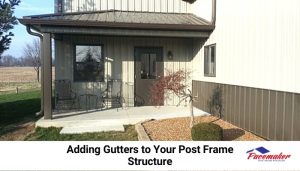
Adding Gutters to Your Post Frame Structure
Keep moisture away from your post frame building and extend it's life. Learn about adding gutters to your post frame structure.
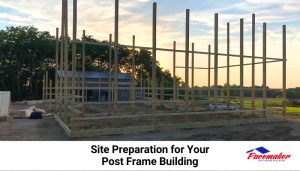
Site Preparation for Your Post Frame Building
Beyond simple leveling and drainage, builders should consider these important factors during site preparation for a post frame building.
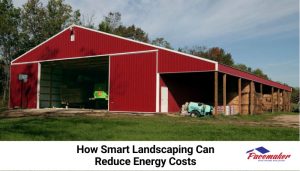
How Smart Landscaping Can Reduce Energy Costs
Aside from construction savings, smart landscaping around a post frame building helps reduce energy costs. Get started by trying these ideas.
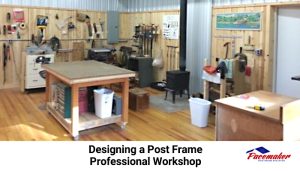
Designing a Post Frame Professional Workshop
Imagine having a professional workshop, a post frame building is a great solution. Use these tips to plan your professional workshop project.
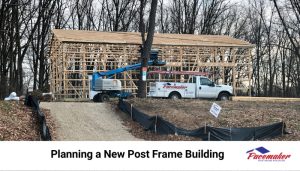
Planning a New Post Frame Building
A post frame building is a great solution for work and storage needs. Here are some helpful tips when planning a new post frame building.
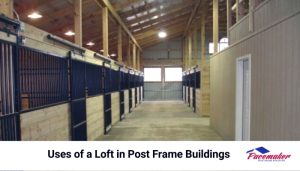
Uses of a Loft in Post Frame Buildings
Loft spaces add more functional space to a post frame building. In this post, we discuss the uses of a loft in post frame buildings.